Construction articles
Don’t let expansion & contraction ruin lighting jobs
By Heath BedalIn landscape lighting, nothing is more exciting than watching the client’s face when they see your vision of their project glow for the first time. And, nothing is more disheartening than hearing their voice when they call to tell you, “The lights stopped working.” It’s a defeating feeling, knowing that your customer who thought so highly of you just a few days earlier, may now think that you’re a hack.
My first call back, almost 25 years ago, was a nightmare. I was sure it had to be bad lamps, cut wires or defective fixtures. I spent hours going over everything, only to find it was several loose connections. I was certain they were tight when I left. What could have caused this?
The root cause of connection failure
After that day I researched connection failure. To my surprise, no one really addressed the root cause of most failures. People had opinions about various connectors, and which were “trash” and which were trusted.I dug deeper and finally learned that the connector is only part of the problem. Yes there are some connectors that should not be used in landscape lighting, or even outdoors. There are also wire or fixture movements that can cause a connection to come undone.
But, the true root cause of most connection failures is the natural expansion and contraction when the connector heats up and cools down. This can be from the environment, repeated cool evenings and warm days. It can also come from poor connection points that build up resistance, creating heat as the system is powered on, and cooling after it shuts down. It also happens in the wire itself. As warming and cooling occurs, the wire jacket expands and contracts, sometimes up to a few inches. This can cause even the tightest connector to come loose.
We’ve all seen them, a bad connection point where the connector is just lying there next to the wires. Contractors get creative to stop this from happening. Often, they try to fix the problem by taping the connectors to the wire jacket, preventing the wires from pulling out of the connectors. (Pic 1) This works, but the cost is added time, and a connection point that stands out in the landscape.
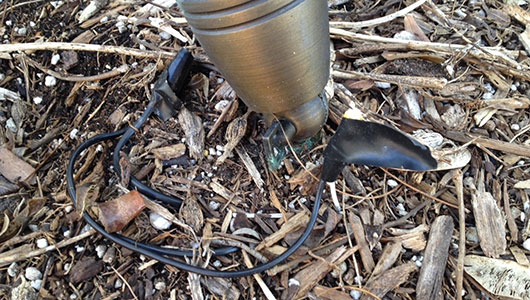
Pic 1 – Connectors wrapped in electrical tape – not a professional look.
Tips to stay connected
Here are a few tips to make better wire connections, reduce call backs, save money and keep that respectable, professional reputation with your customers.- Always use the correct size connector. Undersized connectors will quickly become dislodged. You might think you're saving money by using a smaller connector, or by using what you already have on the truck, but whatever you saved is lost in a single call back.
- Never use a piercing connector. I’m talking about the type that pushes a pin or tooth through the wire jacket. The same expansion and contraction issue will cause that small piercing in the jacket to enlarge and shrink, allowing moisture and air to enter the wire. This will quickly cause corrosion and create a poor connection.
- Always use a connector that was designed:
- for outdoor use,
- for direct burial,
- and with built-in waterproofing. (Never rely on “adding” waterproof material.)
- Don’t strip the wires longer than the recommended length for the connector. If too much copper is exposed, it will not be covered by the connector or its waterproof material.
- Always, no matter what connector you use, “fan” then “twist” your copper wire together. Never just strip and twist the ends of the wire. Strip the wire, then fan the copper strands out for all wires you are connecting. Lay the multiple wire fans on top of each other, and then twist the fans together. (Pic 2)
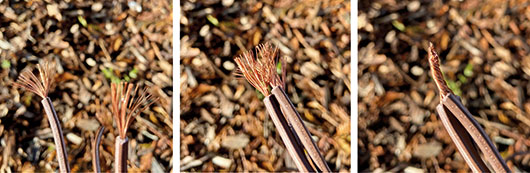
Pic 2 – 1) Fan copper strands. 2) Overlay wire fans together. 3) Twist the fans together.
- If you think you need to use electrical tape, then you’re using the wrong connector. Also, electrical tape is an eyesore in the finished landscape.
- Always use a connector that relieves stress/tension from the copper connection point to the outside of the connector. The connector should hold on to the wire jacket, eliminating the possibility of the connector being dislodged due to expansion and contraction, or fixture and wire movement. (Pic 3)
Heath Bedal is the owner of NewLite Specialty Products, and a part of the lighting industry in Northern California for decades. After years of issues with wire connectors, he developed the Q-Loc™ wire connector. His mission has been to help contractors fix these issues in an easy and affordable way. Visit LandscapeConnector.com or NewLiteProducts.com
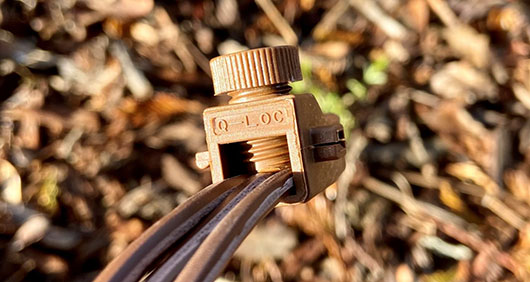
Pic 3 – Use waterproof direct-burial connectors designed to withstand expansion and contraction, or fixture and wire movement.