Articles written by guest contributors
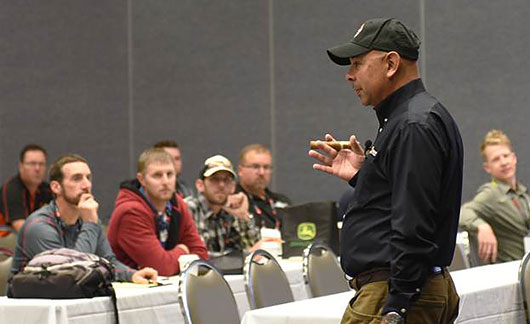
Set up foremen for success
By Frank GandoraThere are job profits and there are company profits. Things happen on the jobsite that directly affect company profits. The people working on the jobsite are major components that affect job profits. Without job profits, there are no company profits.
Material quantities and prices, dimensions and drawings, all these things can be accurately performed and calculated ahead of time, in black and white, on paper. The issue I have experienced is that while an owner or project manager/estimator is haggling with their supplier negotiating that extra nickel savings on a product for a particular project, their crew is miles away on site wasting dollars on that same stuff that you're trying to squeeze pennies out of.
How do you supervise your jobsite crew? Who trains them and leads them day in and day out? For my company, it’s my jobsite foreman. The foreman has the most important and stressful job in the company. Not only do they have to have the experience and skill to layout and successfully build a project, but they must also have the skills of people management.
They have to take direction from their employer, and they have to deal with the client, the delivery people, other trades, inspectors and the various personalities of the crew they are in charge of. To top that off, the foreman is in charge of safety, production, material management, equipment, timekeeping, schedules and keeping an eye on the weather. Typically they are also the ones that have to drive the crew and pull trailers to the jobsite.
We sometimes forget how important our foreman or lead man is to the successful performance and installation of a project. What do you provide to your foreman that will help them with their job? Do you think that a new truck is the answer? What about a big fat raise or bonus? Will those things make your leader more productive and work faster, harder and smarter? Probably not.
The most important thing you can do for your foremen is to find ways to help them deal with the day-to-day stress of running a jobsite. I can tell you now, they are the most stressed-out employees in the company.
The pre-job morning huddle
I find that it boils down to understanding the psychology of the crew. It starts with the foreman taking control of his crew immediately, first thing before the crew even gets to the jobsite. I encourage my foremen to spend time with their crew, off-site in a quiet place. Maybe it is in the back office, the corner of the shop, or at the tailgate of the truck. We call this the morning huddle.At the morning huddle, the foreman shares the plans and specs with their crew before they get to the site. This allows them to share the project with everyone. I have seen crewmembers on jobsites that don’t have a clue as to what the end result is for the tasks that they are asked to do.
Explaining the job upfront, showing them the drawings, and telling them what the finished project will look like gives the crew a sense of being part of the team. It lets them know that their work is contributing to a desired goal. This meeting is a great opportunity to assign specific jobsite tasks and to let each crew member know what is expected of them.
Post a copy of the drawing
When they get to the jobsite, a copy of the drawing is displayed, typically taped up to a window if it is at a house, or on the jobsite trailer, anywhere where everyone on the crew can easily see it every day.We don’t expect the crew to know all the processes, details and methods of construction. We want them to know what the finished product will look like and it gives them an idea of what they are doing and why their tasks are important to the completion of the project.
Do a daily morning huddle
Each morning, before anyone walks on the site, it is a good idea for the foreman to perform a quick 5-minute safety talk. Perhaps it’s a PPE safety check, maybe it's pointing out jobsite hazards, or maybe it is asking crew members if they see any safety issues that need to be addressed and shared with the others.This morning huddle is a pre-work meeting where the foreman can remind the crew of the schedule, tell them what needs to be finished by the end of the day, and inform them of any changes.
Huddle at the end of each day
At the end of each day, the foreman should conduct a post-work huddle meeting before everyone gets back into the truck. The foreman can recognize the crew and its members for a job well done, ask for improvement ideas, and share what was done successfully and what slowed them down.Perhaps the crew has ideas they would like to share. This is also a good time to discuss what tools and equipment will be needed the next day. Let the crew members get involved in the planning and thinking process for the next day. This creates buy-in and motivation by empowering them to be part of the project.
These little talks also put the foreman in a position of authority, sub-consciously taking control while also showing the crew that he cares about their safety and well-being.
Frank Gandora CCPI, CS, PICPS is President of Creative Hardscape Company in Lakewood, CO. Frank is also a certified hardscape trainer and a regular seminar presenter at Hardscape North America.