Contractor Stories
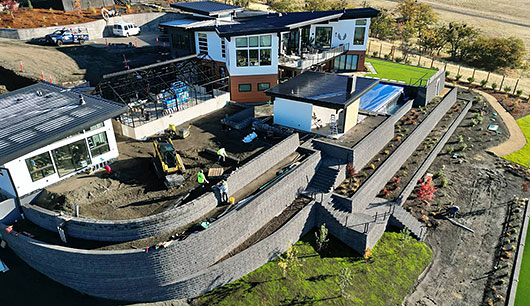
Both the walls and steps are VERSA-LOK Standard, Jason’s favorite SRW block – especially for a job like this with lots of stairs. He says it's easy to make elevations come out right because the wall block and the stair risers are manufactured in the same increments. They make a 6” riser and a 12” step.
“And, we don’t have to buy specialty blocks like 90s for our stair steps. The blocks are solid, so we just break them in half and we create our own 90s.”
“And, we don’t have to buy specialty blocks like 90s for our stair steps. The blocks are solid, so we just break them in half and we create our own 90s.”
Wall job grows from 1,100 to 11,000 face feet (not a typo)
By Tom HatlenContractor Jason Myers says he went to an initial site visit for a project specced at 1,100 face feet of segmental retaining walls. “But after we got there and started talking, I explained that wasn't realistic for all of the things that they wanted to do on that hill without more walls to support it.
“And then as we went along, the client liked the way the SRWs looked compared to the cast-in-place walls planned for other parts of the project. They're more economical than cast-in-place too, so our walls were substituted and the job grew substantially.
“I had slotted a month and a half for the original plan, and we were there for 2 years pretty much year-round.
Project Profile
Oregon hillside home
2023 HNA Award Winner – Segmental Retaining Walls - ResidentialSRW contractor
JM Construction Inc., Shady Cove, ORJason Myers, President
Structural engineer
Structural Solutions, Inc., Medford, ORGeneral manager
Michael C. Woods Construction LLC, Medford, ORProject scope
11,000 face feet VERSA-LOK® Standard19,000 tons 3/4” minus aggregate brought in
1,165 tons 1-1/2” drainage rock brought in
14,000 tons spoil removed
In-house work
Segmental retaining walls, landscape excavation & grading, drainage work, wall lightsWork done by others
Residential home excavation, low voltage lighting, landscaping, pavers, poured in-place concrete walls, hand railsYear completed
2023Few distractions
Jason says, “We don’t get much snow where we would have to pull off the job. But, we did have an occasional week or 2 where we would have to jump to do something else for another customer. But for the most part, we were there pretty steady for 2 years.”While the project was sizeable, Jason kept the crew size to 3 or 4 people on the ground in addition to a truck driver dedicated to the job. They frequently brought in a 2nd truck driver to help out. “I run fairly small crews because I’ve found that the more people you have on a project the harder it is to keep the quality up.”
Jason also runs a 2nd crew of 3 to 4 people.
Doing bigger and bigger walls
JM Construction got the job thru a landscape architect they’ve worked with for 25+ years. Jason says, “She gave us the lead. I met with the client and we came to terms. It was pretty straight forward.”He says they’ve done a lot of good sized jobs, but none compared to the size of this one – until now. “We're doing one now that's even bigger than this one. We do the majority of the segmental retaining walls in this area, so the same architect asked us to do this new project.”
Walls fit with site development
Jason says JM Construction is primarily a site development company. SRWs make up 30% to 40% of their work. “We’ve found a niche in building walls. So anytime we can, that's what we lean towards. We also do house pads, roads, underground work, all types of site work.”Like other site work, the majority of their wall work is excavation. “The building of the wall is the shortest part of the process because you spend so much time doing all the excavation for it and all the backfill. It's basically excavation work and stacking blocks in front of it.”
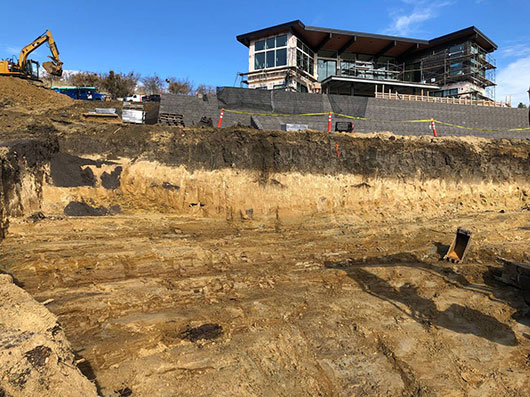
Jason says much of the soil in this part of southern Oregon is what they call black sticky. “It's highly expansive clay, and you can't build on that. So we had to take all of that clay out of all the structural areas. We did a lot of excavation.”
They excavated down to the tan sandstone material (pictured) which is suitable for building.
They excavated down to the tan sandstone material (pictured) which is suitable for building.
So it begins
JM Construction started work not long after the house foundation was in. “That was when I realized that when they excavated for the house, they had pushed a whole bunch of spoil below the house where the swimming pool and all those walls were going to go.“That's kind of standard when someone else is coming in to cut the pad for the house. They just want to get the material out of their way, and most of the time they push it in where people want their patio. So we have to dig it all back out and charge for that.”
But, overall, Jason says working with the other contractors on site went really well. “The site was large enough we didn’t get in each other’s way. I've worked with most of them through the years. Our area is small enough that you kind of know everybody. The general contractor was relatively new to the area, but he was excellent to work with. He wasn't micro managing us all the time.”
“The landscapers, we were working right with them, moving rocks and topsoil and some of their trees for them. They were landscaping each area as we finished up our work there. They kind of chased us up the mountain. Everything we got ready for them, they were landscaping.”
Tall walls buried deep with lots of geogrid
JM Construction’s work involved building walls as high as 11’ above ground and typically 9’ geogrid. There are 9 terraces. The lowest part of the project is the 11’ tall putting green wall buried 4’ to make it structurally sound to hold up the walls above it.The longest stretch of geogrid is 15’ and runs beneath the swimming pool. Jason says, “The engineer wanted the swimming pool to sit on the grids to spread out the load and stabilize the mountain.”
In addition to the structural engineer (Structural Solutions) Jason brought in a geotechnical engineer (Marquess & Associates, Inc.). The geotechnical engineer did nuclear compaction testing behind the walls to ensure everything was at least 95% of Standard Proctor.
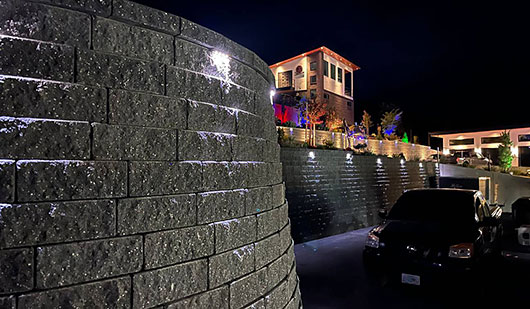
Making the grades
With so many terraces, Jason says the toughest part of the project was trying to make all the different grades. “We had a greenhouse, the little guest house, the swimming pool, the putting green, all those different things. They weren't all at the same grade, and so we had to get creative.”“It's so steep with a 30% slope the water gets traveling so fast, it will cut into the hillside. That had me up at night a little bit. We even had to design an underground detention system with a disbursement pipe at the bottom so we could hold the water and slow it all down. Water is the driving factor on these projects.”
Jason says the client was high energy and detail oriented while also trusting in their expertise to make the project a reality. “She thought through everything. They have solar. They have a propane generator back up. They drilled a well in case something happens with the city water. There’s a greenhouse because she grows a lot of food and things. It was nice to see her vision come together like that.”